Optimizing CIP Systems in Biopharmaceutical Manufacturing
FDO Series Sanitary Regulators Improve CIP Cycle
In large biopharmaceutical facilities, central Clean-in-Place (CIP) systems play a crucial role in maintaining hygiene by supplying cleaning fluids to various process skids across the plant. These skids include chromatography systems, tangential flow filtration (TFF) units, ultrafiltration (UF) equipment, and bottle-filling stations. The CIP system distributes sanitizing fluids where needed, ensuring a controlled and efficient cleaning process.
A key objective of CIP cleaning in sanitary applications is to achieve a target fluid velocity (ft/sec) for a specified duration. In smaller piping systems, this requires relatively low fluid volumes, while larger-diameter pipes demand significantly higher volumes. As a result, process skids may require a broad range of flow rates (lpm/scfm) to reach the necessary cleaning velocity.
The Steriflow/Equilibar FDO Advantage
The FDO fluid control valve is specifically engineered for sanitary applications that demand precise regulation across a wide range of flow rates. Unlike conventional flow control valves (FCVs) that typically manage a 15:1 flow range, the FDO excels with an impressive 100:1 control ratio. Additionally, depending on how the control system is configured, the FDO can regulate either flow rate or pressure, offering exceptional flexibility.
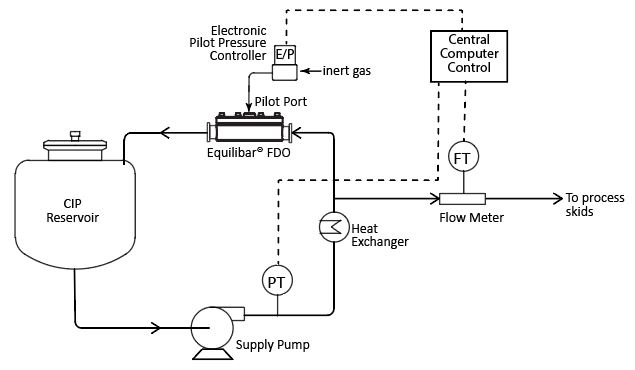
Enhanced CIP Flow Control
In the schematic shown, the CIP system operates in a recirculating loop, integrating an FDO valve, a high-resolution flow meter, and a pressure transducer. A central computer system manages the process, enabling seamless automation. During normal operation, the system recirculates water through a heat exchanger, keeping it ready for the next cleaning cycle.
As different skids request CIP cleaning, the system must rapidly adjust fluid flow rates to meet demand. The FDO’s unique multiple-orifice design and diaphragm-based control allow it to respond within milliseconds to new flow setpoints, ensuring a smooth transition.
When one cleaning cycle concludes and another begins—often requiring a different flow rate—the system must quickly adapt to maintain optimal cleaning velocity. Traditional valves may struggle with slow setpoint adjustments, leading to unstable flow during transitions. However, the FDO can instantly switch between flow and pressure control, minimizing instability and shortening transition times. This efficiency not only reduces cleaning cycle durations but also lowers operational costs by improving overall process effectiveness.
Quick Quote
Know what you need and want a quote quickly? We can help! Fill out this form and we will get back to you shortly.