Optimizing Tank Blanketing in API Pharmaceutical Processing
Key Design Considerations for Inert Gas Blanketing
In Active Pharmaceutical Ingredient (API) manufacturing, raw materials, intermediates, and excipients often require protection from oxygen and moisture to maintain stability and prevent unwanted reactions. One of the most effective solutions is tank blanketing, where an inert gas—typically nitrogen—is introduced into the process tank to displace reactive elements.
Beyond protecting sensitive compounds, nitrogen blanketing (also known as nitrogen padding) enhances safety by reducing the risk of explosion when handling flammable volatile compounds.
Critical Factors in API Tank Blanketing System Design
API pharmaceutical processing presents unique challenges compared to biopharmaceutical applications, requiring careful system design. Key factors to consider include:
- Flow rate of nitrogen gas – Ensuring the correct volume of inert gas enters the system as needed.
- Precise pressure control – Maintaining optimal pressure to suppress solvent evaporation.
- Automation capabilities – Adapting to changing process conditions with minimal manual intervention.
- Chemical compatibility – Managing exposure to corrosive or volatile gases, which may necessitate Hastelloy or other exotic metal components.
- Cleanability standards – Meeting CIP (Clean-in-Place) or SIP (Steam-in-Place) requirements for pharmaceutical environments.
- ATEX compliance – Ensuring equipment meets hazardous area requirements when working with explosive vapors.
How Tank Blanketing Systems Work
A well-designed nitrogen blanketing system precisely regulates the flow and pressure of nitrogen to maintain a stable inert environment inside the tank.
- A pressure-reducing valve (PRV) or tank blanketing valve supplies nitrogen gas until the tank reaches the desired pressure.
- When the pressure exceeds the setpoint, excess gas must be vented. This is where a back pressure regulator (BPR) or “de-padding” regulator ensures proper pressure relief.
- The system continuously adjusts to maintain stability, preventing oxygen intrusion while controlling evaporation and pressure fluctuations.
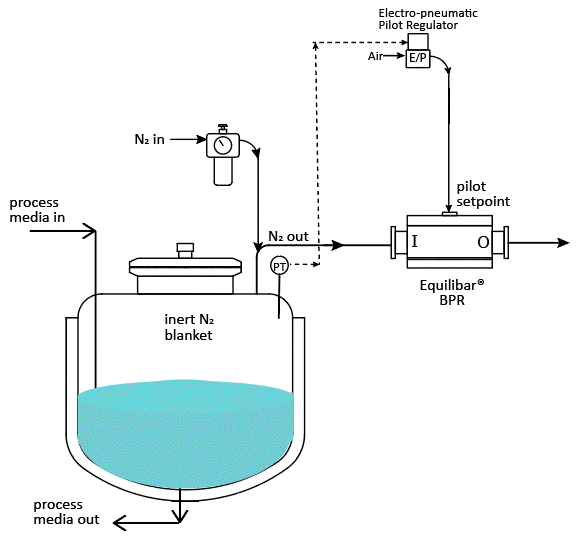
Why Choose Steriflow/Equilibar Back Pressure Regulators for API Tank Blanketing?
Equilibar back pressure regulators (BPRs) offer several advantages in API pharmaceutical blanketing applications:
- Customizable for API Processing Needs – Configured to match specific process parameters.
- Corrosion-Resistant Materials – Available in Hastelloy for handling aggressive volatile gases.
- Ultra-Low Pressure Control – Offers superior precision at low pressures (inWC/mbar) without overpressure spikes.
- CIP/SIP Compatibility – Designed for easy cleaning and sterilization.
- Flexible Control Options – Can be manually or electronically controlled to suit automation needs.
- ATEX Compliance – The pilot setpoint regulator can be selected to meet ATEX safety requirements and placed outside hazardous zones.
- Instantaneous Response – The multiple-orifice diaphragm design allows the valve to adjust seamlessly to pressure fluctuations, eliminating hysteresis and cracking pressure issues seen in traditional spring valves.
- Wide Flow Rate Range – Unlike conventional valves, Steriflow/Equilibar BPRs provide exceptional Cv rangeability, making them ideal for both high and low flow conditions.
Conclusion
For API pharmaceutical tank blanketing, Steriflow/Equilibar BPRs deliver unmatched precision, flexibility, and reliability. Their advanced design ensures optimal pressure control, process safety, and efficiency, making them the preferred choice for inerting and pressure relief in API manufacturing.
How Can We Help You With Your Sanitary Processes?
Learn more about how our Back Pressure Regulators can protect your sanitary process.