What Is Sanitary Balanced Port Thermostatic Steam Trap Operation?
Why do SIP temperature validation alarms, or faults, occur? How does thermostatic steam trap operation affect the occurrence of temperature validation faults?
Most validation temperature alarms can be traced to a single root cause: condensate back up upstream of the steam trap. The condensate forms because of the operating nature of sanitary steam traps, and the design of the tubing where they are installed.
To begin, let’s briefly review the operating principles of sanitary balanced port thermostatic steam traps before we answer the questions above.
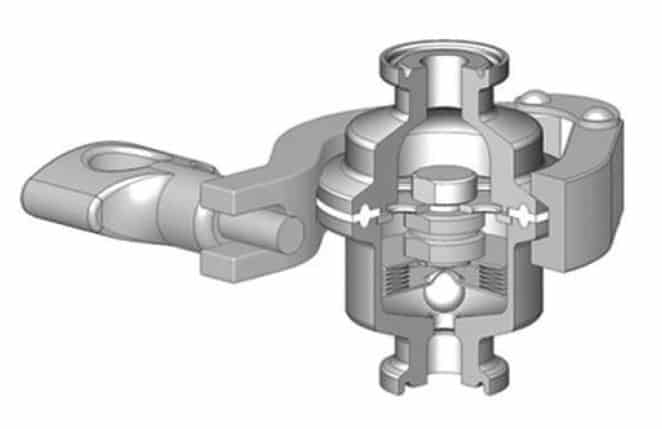
Thermostatic traps operate like a thermostat. As such, they are designed to close when the bellows senses saturated clean steam temperatures, preventing it from passing through the trap. Hence the name “steam trap”. The closure occurs because the volatile, proprietary liquid alcohol fill inside the bellows vaporizes when it is exposed to clean steam temperatures. Pressure builds up inside the bellows expanding it and driving the attached plug (ball or conical tip) into the orifice at the trap outlet. The trap will stay in that closed position until the bellows temperature falls below saturation temperature. When that happens, the bellows will contract as the alcohol vapor condenses, lifting the plug off the seat, releasing any clean steam condensate that has collected upstream of the trap. The steam temperature value when the bellows contracts and the trap begins to open is called it’s subcooling value.
Most validation temperature alarms can be traced to two root causes. They are both related to condensate back-up upstream of the steam trap.
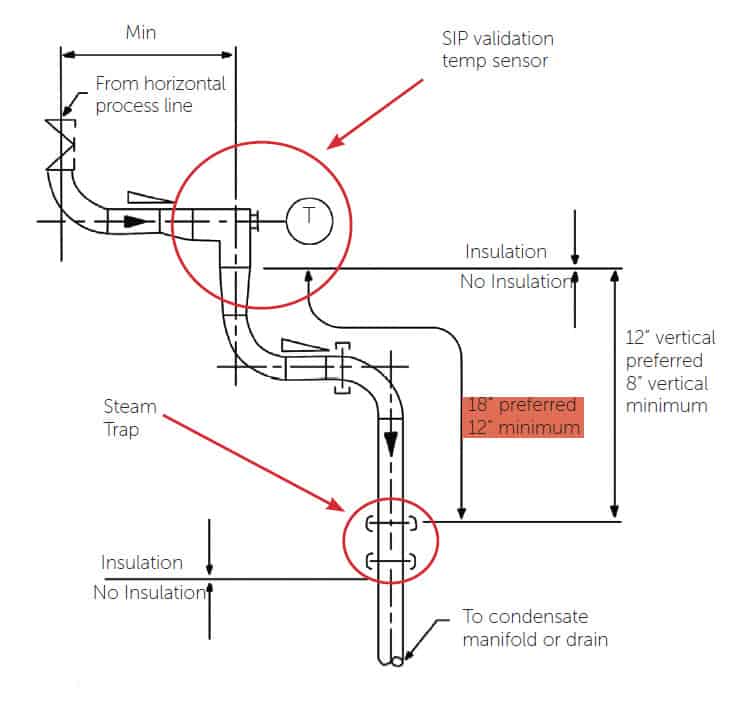
All sanitary thermostatic traps require that a minimum length of tubing be installed between the trap inlet and the validation temperature to account for this buildup of condensate. See illustration above. The standard distance that has been adopted in the industry is 12″ – 18″ (~ 300mm – 450mm). If a thermostatic trap requires significant subcooling before the bellows begins to contract and open the trap, clean steam condensate will back up and build in the tubing upstream of the trap (1) and may wet and cool the validation temperature sensor. If that occurs during (after the system heats up to > 250°F (121°C), a temp validation alarm will occur if the sensor is cooled by 1/2°C or more. High subcooling trap operation is one of the two most frequent causes of validation temperature alarms caused by condensate back up.
Subscribe to Steriflow's Blog!
Be one of the first to watch new how-to videos, read published articles, and hear from experts about all things related to sanitary processing systems.